Corrective Action & Incident Response Management Program
Compliant with 21 CFR §117.150 – Corrective Actions and Corrections
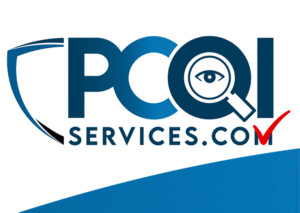
To develop, implement, and maintain a written Corrective Action Procedure (CAP) in alignment with FSMA’s Preventive Controls Rule (21 CFR §117.150), ensuring timely identification, documentation, and resolution of deviations or food safety incidents that affect preventive controls or product integrity.
Deliverables
1. Written Corrective Action Procedure (CAP)
- • Step-by-step procedure for identifying, managing, and documenting non-conformances
- • Includes defined escalation process for high-risk deviations (e.g., environmental pathogen detection)
2. Root Cause Analysis Template & Workflow
- • Structured form and guidance for evaluating failures in preventive controls or verification steps
- • RCA triggers based on product testing failures, incomplete monitoring logs, or audit findings
3. Corrective Action Logs & Records Package
- • Editable CAP logbook and template to record actions, dates, personnel, and product disposition
- • Includes verification step tracking and record review checklist
4. Unanticipated Food Safety Event Protocols
- • Workflow to respond to failure of the food safety plan or unforeseen food safety problems
- • Action plan to re-evaluate product disposition and trigger reanalysis of the food safety plan (per §117.170)
5. Correction Guidance & Templates
- • Definition and documentation tools for quick corrective actions that don’t require full CAP (e.g., allergen labeling corrections, sanitation issues)
- • Pre-written scenarios for common low-risk corrections to streamline decision-making
6. Food Disposition and Evaluation Form
- • Decision tree and documentation tool to evaluate affected product under §402 (adulteration) and §403(w) (misbranding) of the FD&C Act
7. Staff Training Materials: Corrective Action Response
- • Onboarding and refresher deck on how to detect, escalate, and document issues
- • Scenario-based quiz and checklist for QA and line supervisors
Fees and Subscriptions
Initial Setup Fees
Plan | Description | One-Time Fee |
---|---|---|
CAP Lite | 1 corrective action plan template + logbook | $650 |
Standard Incident Response Pack | Full CAP program + training + food safety reanalysis trigger tool | $1,500 |
Comprehensive CAP Suite | Includes RCA tools, CAP/Correction integration, and food disposition support | $2,800 |
Monthly Maintenance Fees
Plan | Monthly Maintenance | Monthly Fee |
---|---|---|
Standard | Quarterly incident review support + minor template updates | $250/month |
Premium | Monthly review of CAP logs + RCA support + retraining access | $500/month |
Enterprise | Incident investigation support, real-time CAP guidance, compliance alerts, and food safety plan reanalysis support | $850/month |
Monthly Maintenance Coverage Includes
- • Review and feedback on submitted corrective action reports
- • Root cause analysis consultation and corrective/preventive action refinement
- • Monthly summary of trends, repeated incidents, and improvement suggestions
- • Update of CAP templates based on FDA guidance or internal audit findings
- • Support for food safety plan reanalysis when required (per §117.170)
- • Email and chat access for urgent compliance queries or incident reporting
Ideal For:
- • Facilities with ready-to-eat (RTE) foods and pathogen monitoring requirements
- • Manufacturers preparing for FDA audits and needing proactive incident management
- • QA teams requiring structured response to food safety deviations or failures
- • Private labelers and co-manufacturers who need documented corrective action responses for client assurance